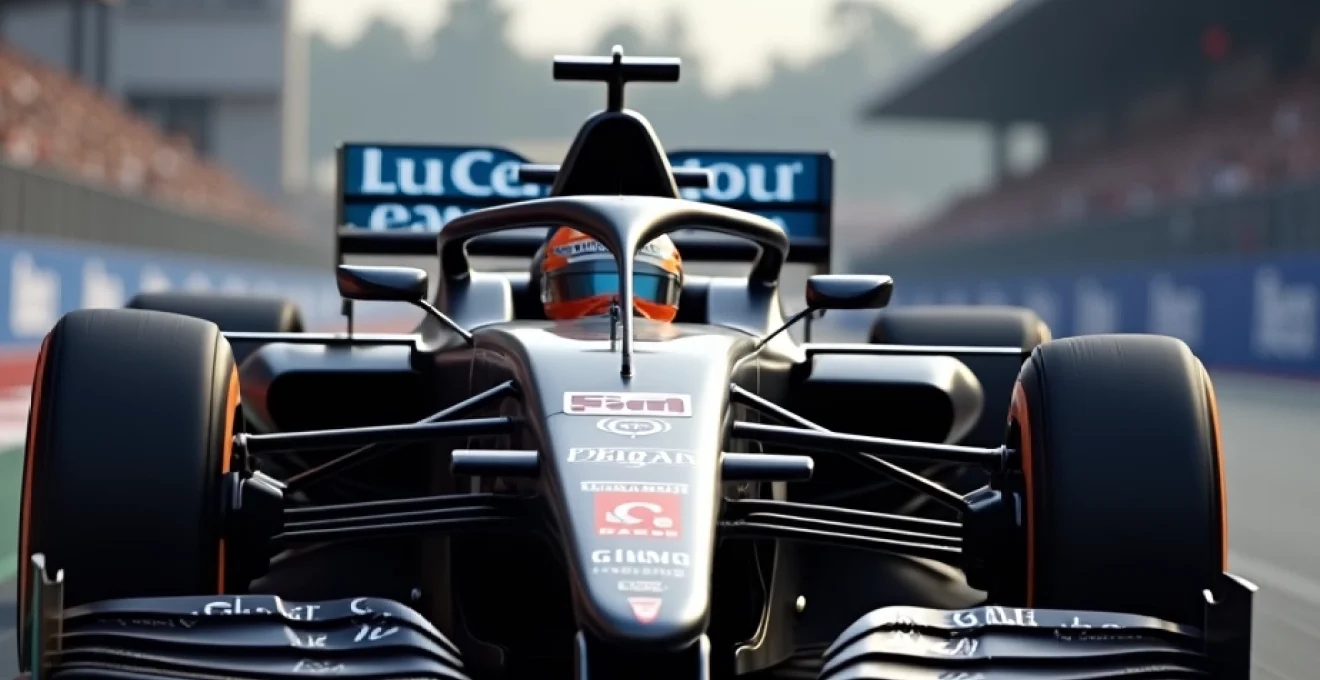
In the high-octane world of competitive racing, car engine performance stands as the cornerstone of success. The relentless pursuit of power, efficiency, and reliability drives teams to push the boundaries of engineering and innovation. From Formula 1 to NASCAR, the quest for that extra horsepower or fraction of a second improvement can mean the difference between victory and defeat. This intense focus on engine optimization has led to groundbreaking technologies that often trickle down to consumer vehicles, making racing a crucible of automotive advancement.
Engine optimization techniques for competitive racing
The art and science of engine optimization in racing is a complex dance of physics, chemistry, and engineering. Teams employ a variety of techniques to extract maximum performance from their powerplants while adhering to strict regulations. These methods often involve fine-tuning every component, from the combustion chamber design to the exhaust system.
One key area of focus is volumetric efficiency, which measures how effectively an engine can move air through its cylinders. By improving this metric, engineers can significantly boost power output without necessarily increasing engine size. This is achieved through careful design of intake and exhaust ports, valve timing optimization, and the use of advanced materials that can withstand higher temperatures and pressures.
Another critical aspect is thermal management. Racing engines operate at extreme temperatures, and controlling heat is essential for maintaining performance and reliability. Advanced cooling systems, thermal coatings, and precision-engineered components all play a role in keeping temperatures in check while allowing the engine to operate at peak efficiency.
Power-to-weight ratio: key performance metric
In the world of competitive racing, the power-to-weight ratio reigns supreme as a key indicator of a vehicle's potential performance. This metric, which measures the amount of power available per unit of weight, is crucial because it directly impacts acceleration, top speed, and handling characteristics. Engineers and designers work tirelessly to maximize this ratio through various means.
Calculating effective horsepower in race conditions
While dyno testing provides valuable data, the true measure of an engine's performance comes on the track. Calculating effective horsepower in race conditions involves complex algorithms that account for factors such as air density, track temperature, and aerodynamic drag. Teams use sophisticated telemetry systems to gather real-time data, allowing them to fine-tune engine parameters for optimal performance throughout a race.
The concept of brake specific fuel consumption (BSFC) is also crucial in these calculations. BSFC measures how efficiently an engine converts fuel into mechanical power. By optimizing this metric, teams can not only improve performance but also extend fuel range, which can be a decisive factor in endurance racing events.
Weight reduction strategies: carbon fiber and titanium components
Weight reduction is a relentless pursuit in racing, with teams scrutinizing every component for potential weight savings. The use of advanced materials like carbon fiber and titanium has revolutionized this aspect of racing engineering. Carbon fiber, with its exceptional strength-to-weight ratio, is now commonplace in chassis construction, body panels, and even engine components like intake manifolds.
Titanium, prized for its high strength and low density, finds applications in critical engine components such as connecting rods, valves, and exhaust systems. These materials not only reduce overall vehicle weight but also contribute to improved engine performance by reducing reciprocating mass and allowing for higher rev limits.
Balancing power output with fuel efficiency
In modern racing, particularly in endurance events, the balance between power output and fuel efficiency is more critical than ever. Regulations often limit fuel consumption, forcing teams to innovate in engine design and strategy. This has led to the development of highly sophisticated engine management systems that can adjust fuel delivery and ignition timing on the fly to optimize performance under varying conditions.
The rise of hybrid powertrains in certain racing categories has added another dimension to this balancing act. Engineers must now integrate electric motors and energy recovery systems with traditional internal combustion engines, creating powerplants that can deliver bursts of intense power while maintaining overall efficiency throughout a race.
Turbocharging and supercharging in motorsports
Forced induction systems, including turbochargers and superchargers, have become integral to achieving high power outputs in modern racing engines. These systems compress the incoming air, allowing more fuel to be burned and thus generating more power from a given engine displacement. The choice between turbocharging and supercharging often depends on the specific racing category and its regulations.
Variable geometry turbochargers: adapting to track demands
Variable geometry turbochargers (VGTs) represent a significant advancement in forced induction technology. Unlike traditional fixed-geometry turbochargers, VGTs can adjust their internal geometry to optimize performance across a wide range of engine speeds. This adaptability is particularly valuable in racing, where engines must perform effectively from low-speed corners to high-speed straights.
The ability of VGTs to reduce turbo lag and provide more consistent boost pressure throughout the rev range has made them a favorite in many racing categories. Engineers can fine-tune the turbocharger's behavior to match specific track characteristics, providing drivers with responsive power delivery precisely when needed.
Electric superchargers: instant boost for formula E
The emergence of electric racing series like Formula E has spurred innovation in electric boosting technologies. Electric superchargers, which use a high-speed electric motor to compress intake air, offer instant boost without the lag associated with traditional exhaust-driven turbochargers. This technology is particularly well-suited to the power delivery characteristics of electric powertrains, providing rapid acceleration out of corners.
While not yet widespread in conventional motorsports, the development of electric superchargers in Formula E is likely to influence future hybrid and internal combustion engine designs across various racing categories.
Intercooler design: maximizing air density for power
Intercoolers play a crucial role in forced induction systems by cooling the compressed air before it enters the engine. This cooling increases air density, allowing more oxygen to be packed into each cylinder for improved combustion efficiency. In racing applications, intercooler design is a critical area of development, with teams seeking to maximize cooling efficiency while minimizing weight and aerodynamic impact.
Advanced materials and designs, such as air-to-water intercoolers and 3D-printed cores with optimized flow patterns, are pushing the boundaries of what's possible in this field. The goal is to deliver the coolest, densest air charge possible to the engine, translating directly into increased power output.
Boost control systems: precision tuning for race conditions
Modern boost control systems are marvels of precision engineering, allowing teams to fine-tune boost pressure in real-time based on a multitude of factors. These systems can adjust boost levels based on gear selection, throttle position, engine temperature, and even GPS position on the track. This level of control enables engineers to extract maximum performance while staying within regulatory limits and ensuring engine reliability.
Advanced wastegate and blow-off valve designs also play a crucial role in boost control, managing exhaust flow and pressure spikes to maintain optimal turbocharger performance throughout a race.
Engine management systems: precision control for peak performance
The brain behind every modern racing engine is its sophisticated management system. These systems coordinate every aspect of engine operation, from fuel injection and ignition timing to boost control and traction management. The complexity and capability of these systems have grown exponentially in recent years, driven by advances in computing power and sensor technology.
Real-time telemetry analysis in F1 engine tuning
Formula 1 represents the pinnacle of motorsport technology, and nowhere is this more evident than in the use of real-time telemetry for engine tuning. Every F1 car is equipped with hundreds of sensors that continuously stream data back to the pit wall and remote engineering centers. This data includes everything from engine temperatures and pressures to fuel flow rates and exhaust gas composition.
Engineers use sophisticated algorithms to analyze this torrent of data in real-time, making split-second decisions on engine settings to optimize performance. The ability to detect and respond to minute changes in engine behavior can be the difference between winning and losing in the hyper-competitive world of F1.
Adaptive fuel injection mapping for varying race conditions
Modern racing engines employ incredibly precise fuel injection systems capable of delivering fuel with millisecond accuracy. The mapping that controls these systems is continuously refined based on a wide range of inputs, including throttle position, engine speed, air temperature, and even g-forces experienced during cornering and braking.
Adaptive fuel injection mapping allows engines to maintain optimal air-fuel ratios under all conditions, maximizing power output while minimizing fuel consumption. This technology has become particularly crucial in endurance racing, where fuel efficiency can be as important as outright power.
Traction control integration with engine management
While explicit traction control systems are banned in many racing categories, the integration of engine management with vehicle dynamics control has become increasingly sophisticated. Modern systems can modulate engine power delivery based on wheel slip, yaw rates, and other dynamic factors to help drivers maintain control and maximize acceleration out of corners.
This integration requires close cooperation between engine and chassis engineers, as well as drivers, to develop systems that enhance performance without overly interfering with the driving experience. The goal is to provide a safety net that allows drivers to push the limits of adhesion with confidence.
Materials science in high-performance engine design
The relentless pursuit of performance in racing has driven significant advancements in materials science. Engineers are constantly seeking new materials and coatings that can withstand the extreme temperatures, pressures, and forces present in high-performance engines while minimizing weight and maximizing efficiency.
Ceramic coatings: thermal efficiency in combustion chambers
Ceramic coatings have revolutionized combustion chamber design in racing engines. These thin, hard coatings serve multiple purposes: they act as a thermal barrier, reducing heat transfer to the cylinder head and allowing for higher combustion temperatures. This increased thermal efficiency translates directly into improved power output and fuel economy.
Additionally, ceramic coatings can improve surface smoothness, reducing carbon buildup and maintaining optimal combustion chamber shape over time. Some advanced coatings even exhibit self-cleaning properties, helping to maintain peak engine performance throughout long races.
Nikasil cylinder linings: reducing friction in NASCAR engines
Nikasil, a nickel-silicon carbide coating, has become a staple in high-performance engine construction, particularly in NASCAR. This ultra-hard coating is applied to cylinder bores, providing exceptional wear resistance and reduced friction compared to traditional iron liners. The reduced friction not only improves power output but also contributes to better fuel efficiency and engine longevity.
The use of Nikasil allows for tighter piston-to-cylinder clearances, improving ring seal and reducing oil consumption. This technology has proven so effective that it has found its way into many high-performance production engines, demonstrating once again how racing innovations can benefit everyday vehicles.
Advanced alloys: balancing strength and weight in pistons
Piston design is a critical area where advanced materials have made a significant impact. Modern racing pistons are often made from complex aluminum alloys that offer an optimal balance of strength, heat resistance, and low weight. These alloys are carefully formulated to maintain their properties at the extreme temperatures experienced in racing engines.
Some cutting-edge designs incorporate metal matrix composites, which embed reinforcing particles or fibers within the aluminum matrix. These composites can offer even greater strength and wear resistance while maintaining the low weight crucial for high-revving engines.
Aerodynamics and engine performance synergy
In modern racing, the relationship between aerodynamics and engine performance is more intertwined than ever. Aerodynamic design not only affects the vehicle's handling and drag characteristics but also plays a crucial role in engine cooling and air intake efficiency.
Airbox design: optimizing air intake for turbocharged engines
The airbox design in turbocharged racing engines is a critical component that can significantly impact performance. Engineers strive to create airbox designs that provide the smoothest, most direct path for air to reach the turbocharger inlet. This often involves complex CFD (Computational Fluid Dynamics) simulations to optimize flow patterns and minimize turbulence.
Advanced airbox designs may incorporate variable geometry elements that can adapt to different speed ranges, ensuring optimal air flow across the entire operating range of the engine. Some designs even integrate cooling features to help manage intake air temperatures, further enhancing engine efficiency.
Exhaust gas management: leveraging the Coandă effect
Exhaust gas management has become an area of intense focus in racing aerodynamics, particularly in Formula 1. Engineers have found ways to use the high-energy exhaust gases to influence the car's aerodynamic performance, often leveraging the Coandă effect
to direct airflow in beneficial ways.
Careful placement and shaping of exhaust exits can help to energize airflow over aerodynamic surfaces, increasing downforce without incurring a significant drag penalty. This synergy between engine performance and aerodynamics demonstrates the holistic approach required in modern racing car design.
Engine placement: impact on center of gravity and handling
The location and orientation of the engine within the chassis have a profound impact on a race car's handling characteristics. Mid-engine designs, popular in many racing categories, offer superior weight distribution and a lower center of gravity, enhancing cornering ability and overall dynamics.
In some cases, engineers may even angle the engine slightly to optimize weight distribution or to accommodate other design elements such as transmission placement or aerodynamic features. This level of integration between engine design and overall vehicle dynamics exemplifies the comprehensive approach required to achieve success in modern motorsports.
As racing continues to evolve, the synergy between engine performance, materials science, and aerodynamics will undoubtedly lead to further innovations. These advancements not only push the boundaries of what's possible on the track but also drive progress in the broader automotive industry, benefiting everyday drivers through improved efficiency, performance, and reliability.